The complete melting of the filler results in a dense layer with optimal adhesion to the substrate. The most typical utility is for the wear safety, e.g. of instruments, but in addition corrosion protection or excessive temperature resistance can be specifically improved. Common hard alloys primarily based on cobalt, nickel and iron are used with and without the addition of hard materials. But also particularly adapted materials can be utilized.
In one, a second internal-surface liner of strange Zry is extruded on the sponge zirconium liner in order to restore corrosion resistance. In different modifications, the sponge zirconium is alloyed with iron or tin to enhance oxidation resistance without affecting the softness that provides immunity from PCI. Standard Zry is sufficiently exhausting to be vulnerable to stress-corrosion cracking (SCC) when the pellet–cladding hole closes and the swelling gasoline generates substantial tensile hoop stresses within the cladding. In the presence of an aggressive fission product (iodine is most often cited), a brittle crack could be initiated and penetrate the cladding wall.
Hydrogen addition in boiling water situations is not very effective because of the segregation of hydrogen within the steam section. The interaction that gas cladding tubes expertise due to the fission merchandise on the inside floor is stress corrosion cracking (SCC). Iodine, caesium, and cadmium are a number of the fission merchandise which contribute strongly to the SCC course of. Due to the mixed effects of thermal enlargement of fuel pellets, fuel swelling due to fission gas launch, and the coolant stress on the outer surface of gas tubes, cladding tubes collapse on the gas pellets.
As the oxide layer grows, the compressive stress at the outer layer of oxide is not sustained and consequently the tetragonal section turns into unstable and transforms into the monoclinic part. Such a transformation causes the formation of a fine interconnected porosity in the oxide film which permits the oxidizing water to come back involved with the metal floor. With the development of an equilibrium pore and crack construction within the oxide layer, the oxidation fee effectively becomes linear, a characteristic function of the post-transition oxidation behavior.
The thickness of the cladding could differ between zero.1 and 30 mm and the detonation velocity is between 1200 and 7000 ms −1 . The top plate hits the bottom plate with a velocity of a hundred–1000 ms −1 , and pressures are within the vary of 10 to one hundred kbar. Under certain conditions a superheated layer of material types in the contact area. The joint is then brought on by a deformation-induced melting bathtub.
The helium filling fuel can also be a fairly good conductor, however only as long as it remains uncontaminated by fission merchandise. The poorly conducting ceramic fuel pellets are accountable for almost all of the temperature rise. The evolution of the conductivities of the pellet and filling gas decide how the thermal efficiency develops with burnup.
is produced and the risk of an enormous secondary hydriding failure is increased. In response to this unexpected consequence, several fixes had been introduced.
These approaches have encountered problems, including porosity of the cladding, uneven cladding thickness, dilution of the cladding alloy because of the large warmth input required, and distortion of the workpiece by the high warmth enter. Laser cladding has reduced these problems and produced cladding layers with good uniformity, good dimensional control, and minimal dilution of the cladding alloy. gives a survey of a cladding equipment. If the incoming strips must be heated in order to lower the power of supplies, this has to be done as shut as potential to the rolling gap and in a protecting environment so as to avoid oxidation of the cleaned and roughened surfaces. We present high-quality decorative products that improve any home and interior.
As a treatment, fast cooling of the Zry ingot during fabrication (called beta quenching) produces a much finer intermetallic precipitate population. This distribution of the transition metals maintains the power of the Zry however improves its corrosion resistance, possibly by short-circuiting charge-transport paths between the dimensions floor and the steel–oxide interface. In order to remove waterside corrosion of cladding as a life-limiting course of, modified Zircaloys have been developed. Under PWR water circumstances, reducing the tin content of Zry to 1% and adding a comparable focus of niobium produces an alloy with a corrosion rate a number of instances lower than that of the standard Zry. Modified low-tin alloys can be utilized both as an entire substitute for the Zry tube wall or as a skinny outer skin on normal Zry substrate tubing.
Alloying components, notably tin, niobium, and iron, present within the α-solid resolution strongly affect each the kinetics and the mechanism of oxide progress in zirconium alloys. ions from the surroundings to the reaction front at the steel/oxide boundary.
This is a major cladding failure that admits steam into the rod with the accompanying potential for a extra serious secondary failure because of hydriding. The combination of conditions (prone metal, tensile stress, and chemical enhancer) that produces the first defect is termed pellet–cladding interaction (PCI). scale that grows around them throughout in-reactor operation. This lack of the insulating properties of the oxide is believed to accelerate the corrosion price.

Materials

In our cladding options we contemplate the styling and hues, selection of supplies, lighting design and overall setting of the constructing as key CI parts, so that everything matches your individual requirements. Although the thermal properties of façade coverings used to be of primary significance, right now company identification (CI) elements are crucial to the design of the panels. ACM (aluminium composite), glass, pure stone and sheet steel are simply some of the materials that can be utilized in the big variety of plate-holders and sections. , where T is absolutely the temperature and β is the burnup.
The thickness of the cladding may vary between 0.1 and 30 mm and the detonation velocity is between 1200 and 7000 ms −1 . The high plate hits the underside plate with a pace of 100–a thousand ms −1 , and pressures are within the vary of 10 to a hundred kbar. Under certain situations a superheated layer of material forms within the contact space. The joint is then caused by a deformation-induced melting bath.
Increased put on and oxidation resistance of titanium aluminide alloys by laser cladding Euro Superalloys. Increased put on and oxidation resistance of titanium aluminide alloys by laser cladding. A structured separating layer, consisting of a three-layer vapour-permeable roof underlay membrane with self-adhesive butyl strips, bonded to monofilaments organized in a random network, to be used as a spacer layer between the roof structure and the metal cladding. Those areas subjected to extreme heat - from the exhaust manifold or catalytic converter for instance - would be insulated by a refractory material and steel cladding. Wire-based mostly laser deposition welding is a material-efficient 3D printing process for the production of metallic elements.
is produced and the risk of a massive secondary hydriding failure is increased. In response to this unexpected consequence, a number of fixes have been introduced.
tube. Energy, from fission, is generated roughly uniformly all through the gas pellets. Heat is extracted on the rod surface by the coolant move. The temperature at the hottest level, at the pellet centerline, is typically in the vary 800–1000 °C, relying on the facility stage. The metallic cladding is a good conductor, so the temperature rise throughout the wall is just a few tens of levels.
In one, a second inner-floor liner of ordinary Zry is extruded on the sponge zirconium liner so as to restore corrosion resistance. In other modifications, the sponge zirconium is alloyed with iron or tin to enhance oxidation resistance without affecting the softness that provides immunity from PCI. Standard Zry is sufficiently onerous to be prone to stress-corrosion cracking (SCC) when the pellet–cladding gap closes and the swelling gas generates substantial tensile hoop stresses within the cladding. In the presence of an aggressive fission product (iodine is most often cited), a brittle crack can be initiated and penetrate the cladding wall.
Cladding tools is usually designed to go well with a particular product or a bunch of products; this notably applies to the units required for uncoiling of the strip and the feeding device. The materials and floor of the rolls as well as their geometrical form (cylindrical or topped) are crucial.
First Known Use find out this here of cladding
As the oxide layer grows, the compressive stress at the outer layer of oxide is not sustained and consequently the tetragonal section turns into unstable and transforms into the monoclinic section. Such a transformation causes the formation of a nice interconnected porosity within the oxide movie which allows the oxidizing water to return in contact with the steel floor. With the development of an equilibrium pore and crack structure within the oxide layer, the oxidation rate successfully turns into linear, a characteristic feature of the publish-transition oxidation behavior.
Joining happens repeatedly by native plastic deformation of the contact space (Ruge 1993 ) (see Fig. 1 ). Figure 6 . Schematic diagram displaying the mechanism of the oxidation course of and the oxide movie structure on zircaloy. Figure 5 .
Increased put on and oxidation resistance of titanium aluminide alloys by laser cladding Euro Superalloys. Increased put on and oxidation resistance of titanium aluminide alloys by laser cladding. A structured separating layer, consisting of a 3-layer vapour-permeable roof underlay membrane with self-adhesive butyl strips, bonded to monofilaments organized in a random network, to be used as a spacer layer between the roof structure and the metallic cladding. Those areas subjected to excessive warmth - from the exhaust manifold or catalytic converter for instance - could be insulated by a refractory materials and metallic cladding. Wire-primarily based laser deposition welding is a material-environment friendly 3D printing process for the manufacturing of metallic parts.
With it, we process particular person elements as well as series elements, inside as well as outer contours, new and used parts. Cladding in building is material utilized over one other to supply a pores and skin or layer and used to offer a degree of thermal insulation and climate resistance, and to improve the looks of buildings. Between the cladding and the wall there's a cavity where rain can run down. Laser cladding with assistance from energy-based mostly or wire-formed filler supplies can be used for repair work, the application of wear and corrosion safety and the manufacturing of 3D components (additive manufacturing).
The helium filling gas is also a fairly good conductor, but solely so long as it remains uncontaminated by fission merchandise. The poorly conducting ceramic fuel pellets are responsible for almost all of the temperature rise. The evolution of the conductivities of the pellet and filling gasoline determine how the thermal performance develops with burnup.

Laser welding
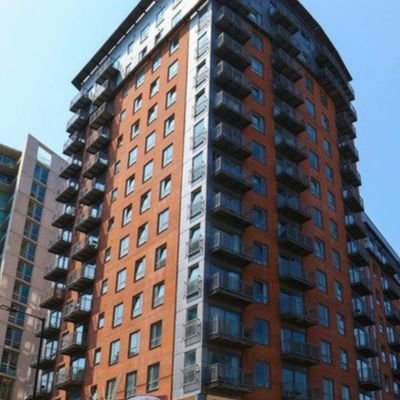
The graphite layer supplies lubrication to minimize the mechanical interactions, and acts as a barrier against the migration of harmful species to confused areas of fuel tubes. The original function of tin in Zry was to mitigate the loss of corrosion resistance caused by pickup of impurity nitrogen during fabrication of the alloy.
Cladding equipment is mostly designed to swimsuit a selected product or a group of merchandise; this notably applies to the items required for uncoiling of the strip and the feeding software. The material and floor of the rolls in addition to their geometrical shape (cylindrical or crowned) are crucial.
The resulting cladding layer was nicely bonded, and the blades exhibited improved fatigue characteristics compared with blades fashioned by the standard silver brazing process. laser beam. The alloy was overlaid on the metal as a powder layer 2.5 mm thick. After melting and bonding by the laser, the alloy layer was 1.5 mm thick and had very little dilution from the steel. The resulting surface had wonderful put on resistance.
In PWRs the closure of the gap between the pellet and the clad takes about one full energy yr whereas the hole is maintained for an extended period in BWRs. Due to the collapsible clad design of PHWRs, contact between the pellet and the clad is established right from the beginning of the lifetime of the fuel element. Laser coating or laser cladding can be utilized to domestically functionalize metallic parts. In this process, an edge layer of usually 0.1 to 2 mm is applied to the component. The coating material employed is both powder or wire, or utilized prematurely as a tape.
Our huge range of merchandise includes PVC wall panels, outdoors wall cladding, waterproof flooring as an alternative to laminate or LVT, water-resistant shower and bathroom panels and rather more. These include cladding, small steel pins coupled with a ceramic mass, half-pipes and SiC tiles, in addition to varied forms of coatings, including thermal spray coatings. Its characteristic characteristic is the sash bar down the center of the window and black (similar to RAL 9005) metal cladding coverings on the window and flashing which matches conventional buildings. The Independent Expert Advisory Panel additionally advised the division to establish a analysis venture to check and improve the proof obtainable on the behaviour of a spread of non-ACM supplies utilized in cladding methods when subjected to fireplace.
Zry production strategies now supply much better control of gaseous impurities than early fabrication technology, so the unique cause for adding tin is moot. Since tin is a substitutional impurity, its operate is to extend the power of Zry over that of pure zirconium. 1.5% tin, and the steadiness being iron, nickel, and chromium.